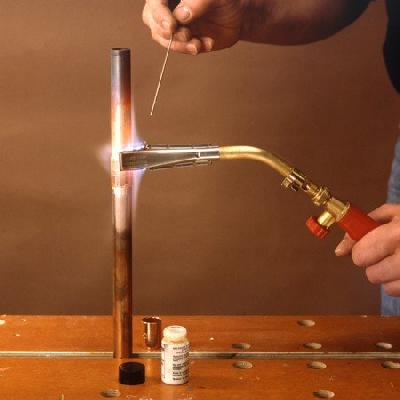
Parmi les procédés d’assemblage par fusion, la technique du brasage est certainement la plus ancienne. Connu depuis la haute antiquité, le brasage a su revenir sur le devant de la scène grâce notamment aux progrès effectués dans l’élaboration de métaux et des méthodes de chauffage. Cette technique est aujourd’hui utilisée dans de nombreuses industries et dans l’élaboration de pièces en métal nobles et aux profils délicats. Découvrez cet article dans le cadre de notre dossier sur le fer à souder.
Ne pas confondre soudage et brasage
C’est en définissant les termes que l’on pourra faire la distinction entre soudage et brasage :
- la soudure est obtenue par fusion des matériaux (métaux de base) et d’un métal d’apport. La plupart des procédés (chalumeau, MIG/MAG, TIG) permettent de gagner des températures correspondants aux point de fusion des matériaux
- la brasure est obtenue par une technique d’assemblage avec métal d’apport sans aller jusqu’à la fusion des métaux de base. La température de fusion du métal d’apport sera inférieure à celle du métal de base.
Deux notions sont essentielles pour aborder le brasage. Le mouillage qui définit la liaison uniforme et sans défauts apparents entre la brasure et la pièce à souder. Enfin, l’effet de capillarité qui décrit le phénomène d'attraction entre la soudure et les pièces à agglomérer.
Comment réaliser une brasure avec effet de capillarité?
La brasure par capillarité est une méthode rapide et économique pour assembler deux pièces de métal. Fréquemment utilisé en plomberie, le brasage permet de souder deux tubes de cuivre. A partir de cet exemple, on vous dévoile les étapes à respecter pour réaliser une brasure par capillarité:
- Après avoir coupé le tube à dimension, éliminer les aspérités dues à la coupe et ébarber les irrégularités, on va frotter les extrémités du tube avec de la laine d’acier ou un tampon de verre. Cette étape a pour but de préparer le tube à recevoir la brasure
- ensuite, on enduit le tube et le raccord d’un flux décapant afin d'éliminer l’oxydation en surface. L’astuce est d’emboutir le raccord sur le tube et de les tourner pour bien répartir la pâte
- enfin, on bloque l’ensemble à l’aide d’un étau et on chauffe la jointure. Quand le métal arrive à la bonne température (ici le cuivre devient rouge vif), on écarte la flamme et on va minutieusement venir déposer l’étain sur la jonction. La température du métal va faire fondre l’étain qui va se répandre dans le joint par diffusion.
A noter que toutes les traces de flux décapants doivent être essuyées après refroidissement car la pâte est très corrosive.
Le brasage tendre
Première des deux techniques de brasage, la brasure dite “tendre” est obtenue lorsque la température de fusion du métal d’apport se situe en deçà de 450°C. L’alliage d’étain généralement utilisé en brasage tendre, entre en fusion à des températures comprises entre 180° et 450°C. De par ces températures basses, il est possible de travailler sur toutes sortes de métaux. Ses limites se situent au niveau de sa résistance mécanique qui est de l’ordre de 5 kilogrammes par millimètre carré. Pour une tenue mécanique supérieure (entre 40 et 50 kilogrammes par millimètre carré) , il faut opter pour la deuxième technique de brasage : le brasage fort.
Le brasage fort
Des brasures obtenues à haute température
Si le brasage fort et tendre ont en point commun le même procédé et l’utilisation de flux décapant, ils se distinguent notamment par la température de fusion des alliages d'apport. De manière formelle on estime qu’un brasage est dit fort dès lors que la température de fusion dépasse les 450 °C. On utilise principalement des alliages de zinc, argent et cuivre dont la chaleur doit atteindre entre 600° et 850°C. Ce distinguo entraîne deux conséquences pour le moins importantes. D’une part, le choix des métaux de base sera limité (leur température de fusion est inférieur à celle du métal d’apport) et d’autre part l’outil de chauffe sera également différent.
Quelle source de chaleur pour du brasage fort ?
Dès lors que l’on souhaite obtenir des températures comprises entre 600 et 850°C, il faut utiliser un chalumeau adéquat. Il existe deux solutions pour deux types de chalumeaux qui sont:
- le chalumeau monogaz qui contient un mélange de butane et de propane optimisé
- le chalumeau bi-gaz ou oxyacétylénique qui utilise deux gaz (l’acétylène et du dioxygène pur) qui permet l’apparition d’une flamme pouvant dépasser les 3000°C.
La soudo-brasure : mode d’emploi
La soudo-brasure a ceci de particulier que la brasure n’agit pas par capillarité mais par accrochage. Soudage hétérogène, le métal de base doit être chauffé à la limite de sa température de fusion afin d’assurer une solidité dans l’ensemble avec des zones d’accrochages importantes. Avec d’excellentes propriétés mécaniques, la soudo-brasure permet d’effectuer des jonctions en “V” ou de travailler sur de la grande épaisseur. La méthode est sensiblement identique à celle du brasage. A savoir:
- nettoyer et décaper les pièces pour les préparer à la soudure
- utiliser un flux décapant pour éliminer les oxydes formés pendant la montée en température
- pour arriver au mouillage, il faut atteindre la bonne température. Les plages vont de 720°C à 900°C. Il faudra l’adapter suivant les pièces à souder. Après avoir déposé le métal d’apport et refroidi la pièce, on essuie les résidus de flux décapant.
- pour une chauffe optimale, le chalumeau mono-gaz n’est pas assez puissant. Il faut donc opter pour un chalumeau oxyacétylénique et obtenir au moins 1000°
- pour les baguettes d’apport, on choisira des alliages de zinc, cuivre, laiton et silicium.
Le brasage a de beaux jours devant lui
Aéronautique, électronique, orfèvrerie ou encore robotique, ces industries ont toutes intégré le brasage dans leur processus de production. La miniaturisation couplée à l’innovation permettent au brasage de surfer sur la vague du progrès et de se renouveler en permanence.